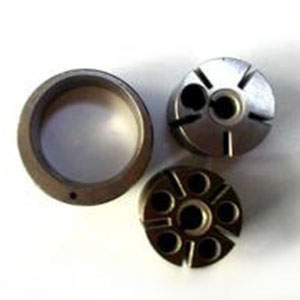
Powder Metallurgy is a process used to make gears from metallic powders of bronze, iron, stainless steel, and alloy steels. These gears are used in electric motors, automobiles, pumps, power tools, and small appliances.
The process usually consists of three steps. During the first step, appropriately fine powder of the selected workpiece material is sourced and may be blended with other powders or binders. This is then followed with a compaction step, usually at room temperature under high pressure, in a die cavity which has the shape of the desired gear. The last step usually then includes the removal of the compacted blank (referred to as the green state) before it is sintered in a furnace. Depending on the required accuracy, the gears may be subjected to a recompaction or coining operation for final finishing. Cylindrical, spur, helical, and other kinds of gears, such as bevel and face gears, can be made by this process.
Powder metallurgy is economical for mass production of gears of sizes ranging from a few millimeters to over 300 mm in diameter. It can produce gear-tooth accuracies of up to AGMA 8. In view of limitations in press capacities and die dimensions, this process cannot be used to produce herringbone gears or helical gears with a helix angle of more than 35°.