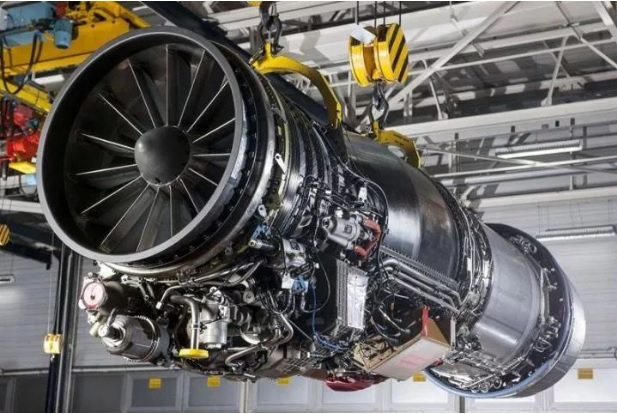
Aero-engine and land-based gas turbine applications
Aero-engine and land-based gas turbine applications for Powder Metallurgy products require extremely good properties and the PM-based process routes in this sector generally incorporate Hot Isostatic Pressing (HIP).
For nickel-based superalloy turbine discs, processing from powders has become necessary to allow the next increments in product performance, through enhanced microstructural control and compositional capability compared with ingot-route material. The Powder Metallurgy process generally involves isothermal forging of a HIP billet, although “as-HIP” parts can also be used where creep strength is the sole design criterion.
Net-shape HIP titanium Powder Metallurgy products have been developed for turbine applications where conventional processing (involving machining) is very wasteful of material and the Powder Metallurgy route can offer cost benefits. The addition of features to forged or cast parts using powder-based additive manufacturing techniques is also being applied for similar reasons.
Airframe sector
Powder metallurgy is a preferred manufacturing process for various structured parts due to its cost effectiveness.
There is also growing interest in the use of Powder Metallurgy in the airframe sector, either for cost saving in applications already using wrought-route titanium or for potential weight reduction in replacing steel parts.