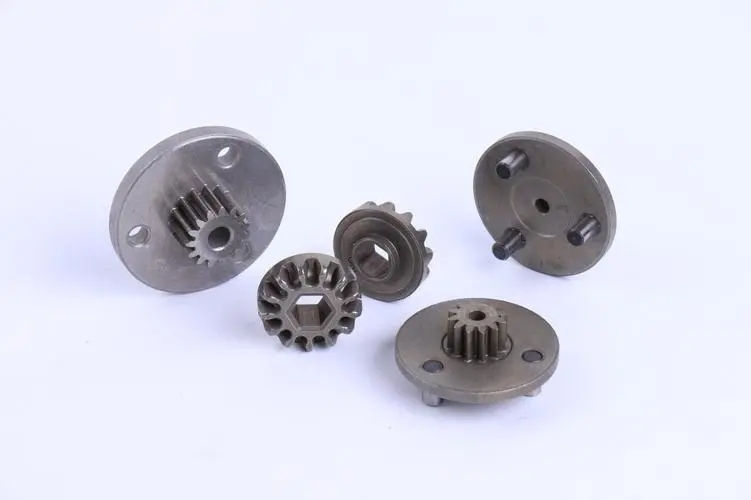
Powder metallurgy (PM) gears are increasingly being used in gear reducers due to their ability to offer excellent performance characteristics while also being cost-effective. Gear reducers, which are used to reduce speed and increase torque in various mechanical systems, benefit significantly from the use of PM gears in several ways:
1. High Strength and Wear Resistance
PM gears can be designed with superior material properties such as high wear resistance and strength. This is particularly important in gear reducers, where gears experience significant load and friction. The material properties of PM gears can be tailored by adjusting the composition of the powder mix, offering better durability over traditional cast or machined gears.
2. Controlled Porosity for Lubrication Retention
One of the key advantages of powder metallurgy in gear manufacturing is the ability to control the porosity of the material. PM gears can retain lubrication within their pores, reducing the friction between the teeth and enhancing the overall efficiency of the gear reducer. This can lead to better heat dissipation and a reduction in the need for frequent lubrication changes, thus improving the maintenance intervals.
3. Complex Shapes and Precision
Powder metallurgy allows for the production of gears with intricate shapes and precise dimensions, which can be difficult to achieve with conventional manufacturing methods. PM gears can be produced with fine surface finishes and tight tolerances, contributing to smooth operation and reduced wear in the gear reducer. Additionally, powder metallurgy allows for the integration of features like teeth profiles and mounting holes directly in the manufacturing process, reducing the need for secondary machining operations.
4. Cost-Effectiveness
Powder metallurgy can be more cost-effective than traditional gear manufacturing processes like casting, forging, or machining, especially for medium to high-volume production. The near-net shape manufacturing of PM gears means less material waste and a reduction in the need for additional machining, which can reduce overall production costs.
5. Material Customization
With powder metallurgy, manufacturers can select and blend different materials to meet specific requirements for the gear reducer. For instance, they can create gears with a high proportion of wear-resistant alloys, such as steel, bronze, or sintered carbide, or they can incorporate additives that enhance properties like fatigue resistance, corrosion resistance, or strength. This customization is particularly valuable in high-performance or specialized gear reducers used in demanding applications.
6. Reduced Noise and Vibration
The material consistency and the potential for controlled porosity in PM gears can lead to quieter operation compared to gears produced using traditional methods. For gear reducers, where noise and vibration can be a concern, PM gears help to reduce operational sound levels, which is especially important in industrial machinery, automotive transmissions, and other noise-sensitive applications.
7. Lightweight and High-Torque Capacity
Powder metallurgy allows for the creation of lightweight gears that still maintain a high torque capacity. This is advantageous for gear reducers where both weight and torque are critical factors. The ability to reduce weight without sacrificing strength or durability can improve the overall efficiency and performance of the reducer.
8. Increased Fatigue Resistance
The manufacturing process of powder metallurgy gears can be optimized to enhance their fatigue resistance. The fine, uniform grain structure and the ability to control the density of the material can improve the gear’s performance in cyclic loading conditions, which is common in gear reducers. This leads to longer service life and reliability under continuous use.