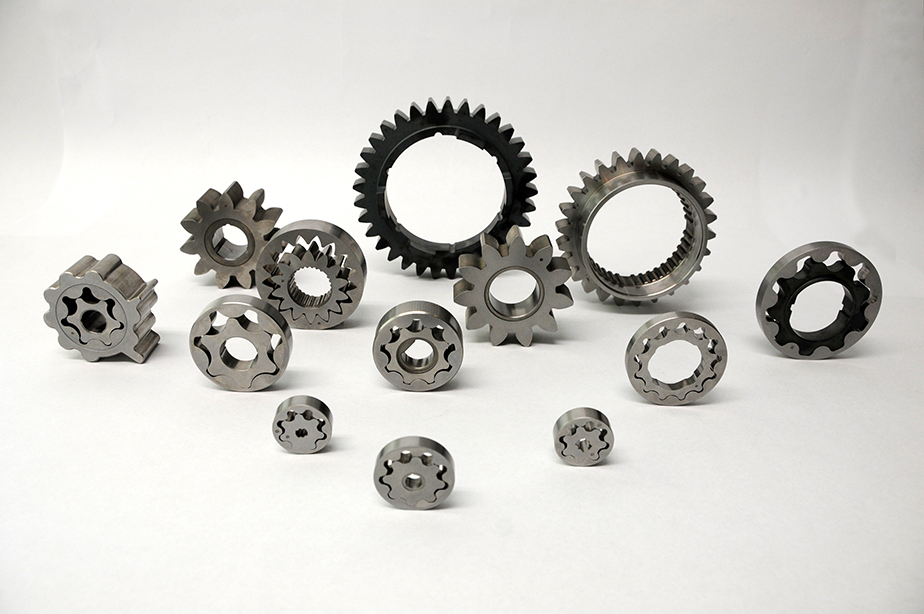
In order to improve the strength and wear resistance of powder metallurgy gears, we usually need to add post-processing engineering after the powder metallurgy gears are sintered to improve their performance. For example, in the post-treatment of powder metallurgy gears, engineers of powder metallurgy gear manufacturers generally use surface water vapor treatment and carburizing treatment to increase the wear resistance and surface hardness of the product. Ordinary FN0205 powder metallurgy gears can carry torque up to 14NM, warm-pressed parts can reach 20NM, if warm-pressed FD0405 can reach about 25, in the case of a complete set of gears using professional powder metallurgy design to allow modification, the slight increase can be increased by 30 -40%.
In the powder metallurgy process, it is very important to control and predict the size change, especially the design of the mold size. One of the major characteristics of the powder metallurgy process is that it can manufacture parts with complex shapes and at the same time obtain near-net-shape parts. Generally, the compact obtained during forming has high precision, but due to the recombination and arrangement of the powder particles during the sintering process, the expansion or contraction of the product is caused, which makes the geometric or dimensional accuracy of the sintered gear and other products reduce.
In the manufacturing process of powder metallurgy parts and powder metallurgy alloy gears, size control or prediction is an important consideration. One of the goals of general sintering is to make the size of the part consistent with the size of the forming cavity. However, the dimensional changes of powder metallurgy products are mainly affected by the characteristics of the raw material powder, forming conditions, sintering temperature and sintering time and other process parameters. These parameters also affect the dimensional accuracy, microstructure and mechanical properties of the finished product.
When the powder metallurgy gear is sintered at the general sintering temperature, the tooth surface is expanded. As the sintering temperature increases, the microstructure of the gear becomes denser, and the expansion of the tooth surface decreases, and even changes from expansion to contraction. The pressure angle of the tooth profile Will gradually become larger. According to the test results, regardless of the expansion or contraction of the gear size, the tooth profile error gradually increases from the root of the tooth to the crown, and the crown part changes greatly, and this change will cause a change in the pressure angle of the tooth profile. That is, when the gear size expands, the tooth profile pressure angle becomes smaller, and when the gear shrinks, the tooth profile pressure angle becomes larger. The sintering temperature of powder metallurgy gears affects the size and tooth profile accuracy of the finished gear. Adjusting the sintering temperature can improve the accuracy of powder metallurgy gears.