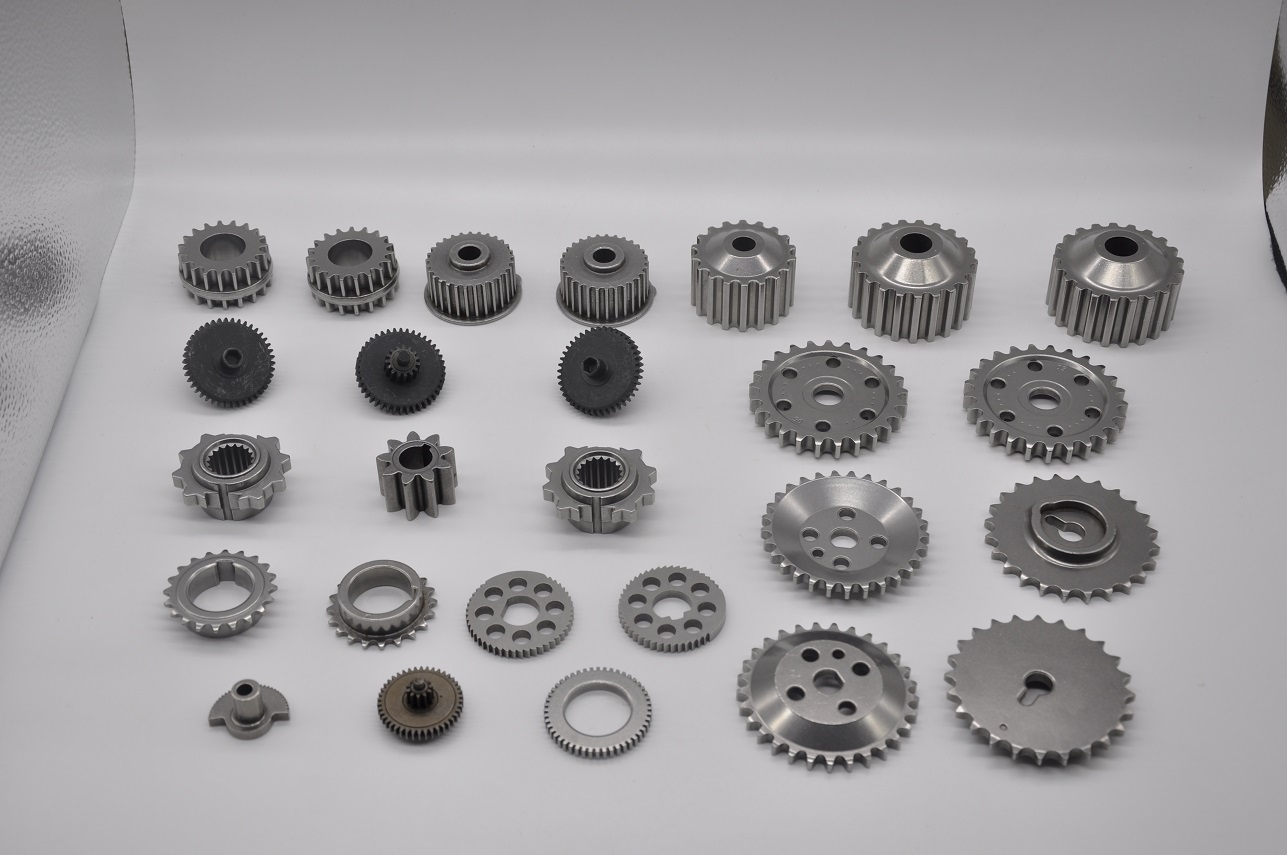
One of the goals of general sintering is to make the size of the part consistent with the size of the forming cavity. However, the dimensional changes of powder metallurgy products are mainly affected by the characteristics of the raw material powder, forming conditions, sintering temperature and sintering time and other process parameters. These parameters also affect the dimensional accuracy, microstructure and mechanical properties of the finished product. The author of this article has discussed the influence of different raw materials on the accuracy of tooth profile in the past. In this article, we will discuss the tooth profile variation of powder metallurgy gears after sintering at different temperatures, and understand the factors that cause tooth profile errors for future gear deformation experiments. Design and analysis of tooth shape variation provide basis.
The sintering temperature of powder metallurgy gears affects the size and tooth profile accuracy of the finished gear. Adjusting the sintering temperature can improve the accuracy of powder metallurgy gears. When the powder metallurgy gear is sintered at the general sintering temperature, the tooth surface is expanded. As the sintering temperature increases, the microstructure of the gear becomes denser, and the expansion of the tooth surface decreases, and even changes from expansion to contraction. The pressure angle of the tooth profile Will gradually become larger. According to the test results, regardless of the expansion or contraction of the gear size, the tooth profile error gradually increases from the root of the tooth to the crown, and the crown part changes greatly, and this change will cause a change in the pressure angle of the tooth profile. That is, when the gear size expands, the tooth profile pressure angle becomes smaller, and when the gear shrinks, the tooth profile pressure angle becomes larger.
In order to improve the strength and wear resistance of powder metallurgy gears, we usually need to add post-processing engineering after the powder metallurgy gears are sintered to improve their performance. For example, in the post-treatment of powder metallurgy gears, engineers of powder metallurgy gear manufacturers generally use surface water vapor treatment and carburizing treatment to increase the wear resistance and surface hardness of the product.